9 методов мониторинга состояния оборудования
Мониторинг состояния состоит из измерения параметров оборудования, которые указывают на неисправность.
Надеюсь, вы сможете вовремя обнаружить изменения в обычных схемах, чтобы предотвратить поломку, сэкономить на реактивном обслуживании и продлить срок службы своего актива. Но так будет, только если выбрать правильные методы мониторинга состояния оборудования и операций.
Мониторинг состояния, конечно же, пересекается с профилактическим обслуживанием, которое нужно для отслеживание поведения активов. Собранные данные служат основой для выявления тенденций и алгоритмов. Однако имеет смысл говорить о мониторинге состояния в режиме реального времени даже без программы профилактического обслуживания.
Мониторинг состояния, IIOT и надежность
Когда дело доходит до профилактического обслуживания, два самых больших препятствия — это требуемые инвестиции и сложность разработки алгоритмов. Но Интернет вещей (IoT) и Промышленный Интернет вещей (IIoT) привели к большим изменениям в отрасли. Датчики и устройства мониторинга состояния теперь подключены к платформам технического обслуживания и предоставляют данные в режиме реального времени.
Это новое подключение является более доступным и простым в реализации, чем профилактическое обслуживание. Актуальные данные позволяют менеджерам корректировать свои планы превентивного сервиса, а также обеспечивают повышенную надежность. В то же время искусственный интеллект может обрабатывать эти сведения для распознавания закономерностей. А это уже одно из самых многообещающих достижений в области надежности с использованием цифровых технологий.
Независимо от того, сможете ли вы сразу же внедрить план профилактического обслуживания, мониторинг состояния ценен сам по себе.
Преимущества мониторинга состояния:
Надеюсь, вы сможете вовремя обнаружить изменения в обычных схемах, чтобы предотвратить поломку, сэкономить на реактивном обслуживании и продлить срок службы своего актива. Но так будет, только если выбрать правильные методы мониторинга состояния оборудования и операций.
Мониторинг состояния, конечно же, пересекается с профилактическим обслуживанием, которое нужно для отслеживание поведения активов. Собранные данные служат основой для выявления тенденций и алгоритмов. Однако имеет смысл говорить о мониторинге состояния в режиме реального времени даже без программы профилактического обслуживания.
Мониторинг состояния, IIOT и надежность
Когда дело доходит до профилактического обслуживания, два самых больших препятствия — это требуемые инвестиции и сложность разработки алгоритмов. Но Интернет вещей (IoT) и Промышленный Интернет вещей (IIoT) привели к большим изменениям в отрасли. Датчики и устройства мониторинга состояния теперь подключены к платформам технического обслуживания и предоставляют данные в режиме реального времени.
Это новое подключение является более доступным и простым в реализации, чем профилактическое обслуживание. Актуальные данные позволяют менеджерам корректировать свои планы превентивного сервиса, а также обеспечивают повышенную надежность. В то же время искусственный интеллект может обрабатывать эти сведения для распознавания закономерностей. А это уже одно из самых многообещающих достижений в области надежности с использованием цифровых технологий.
Независимо от того, сможете ли вы сразу же внедрить план профилактического обслуживания, мониторинг состояния ценен сам по себе.
Преимущества мониторинга состояния:
- Предотвращает крупные поломки и сокращает время простоя.
- Обеспечивает лучшее управление активами на протяжении всего срока их службы.
- Снижает затраты, особенно при аварийном обслуживании.
- Обеспечивает основу для разработки алгоритмов прогнозирования в будущем.
Типы мониторинга состояния
Мониторинг состояния начинается с основных проверок. Небольшие изменения, такие как аномальная температура или давление, странные звуки, чрезмерная вибрация или странный запах, часто являются признаками проблем. Однако методы мониторинга состояния варьируются от самых простых проверок до передовых технологий.
1. Анализ масла
Этот анализ применим к машинным маслам, смазочным материалам и жидкостям. Он может обнаруживать ухудшение качества, перегрев и загрязнение. Например, высокий уровень железа часто указывает на наличие сора и песка. Своевременное обнаружение снижает количество отказов редуктора на 50 % . Предотвращение загрязнения уменьшает вероятность выхода подшипников из строя на 75 % . Окупаемость инвестиций на анализ масла составляет 20:1.
Если вы хотите предотвратить эти сбои, существует несколько доступных методов анализа масла:
Мы ничего не пропустили?
2. Анализ вибрации
Анализ вибрации является одним из самых известных методов профилактического обслуживания. Он может обнаруживать перекосы, дисбаланс и износ примерно за 3 месяца до того, как они приведут к поломке. Это также возможность снизить энергопотребление, поскольку, например, водяные насосы с несоосностью потребляют до 15 % больше энергии . Измерение вибрации также широко используется в ISO 22096 .
Методы мониторинга состояния анализа вибрации включают:
3. Анализ цепи двигателя
Анализ цепи двигателя, также известный (MCA), позволяет оценить состояние электромоторов. Его можно использовать для исследования кондиции (включая роторы, проблемы с муфтой/ремнем, качество электроэнергии), электрического дисбаланса и изоляции. MCA применим не только для предотвращения сбоев, но и для снижения затрат на энергоресурсы и повышения эффективности оборудования на 10–15 % .
4. Термография
Термография изучает распределение тепла и излучения в машинах. Анализ данных делает все остальное, выявляя закономерности, указывающие на отказ или деградацию. Он имеет широкий спектр применений, включая обнаружение несоосности, дисбаланса, неправильной смазки, износа и напряжения в механических деталях. В электрооборудовании он выявляет перегрев, утечки в трубах и слабые места ёмкостей под давлением.
Инфракрасная термография, в частности, стала популярным методом профилактического обслуживания и неразрушающего контроля. Она чрезвычайно эффективна для повышения безопасности, уменьшения количества «слабых точек» и потенциальных причин отказа на 90%. В целом, термография снижает риск, предотвращает сбои и минимизирует затраты и потери.
1. Анализ масла
Этот анализ применим к машинным маслам, смазочным материалам и жидкостям. Он может обнаруживать ухудшение качества, перегрев и загрязнение. Например, высокий уровень железа часто указывает на наличие сора и песка. Своевременное обнаружение снижает количество отказов редуктора на 50 % . Предотвращение загрязнения уменьшает вероятность выхода подшипников из строя на 75 % . Окупаемость инвестиций на анализ масла составляет 20:1.
Если вы хотите предотвратить эти сбои, существует несколько доступных методов анализа масла:
- тесты на наличие воды,
- тесты вязкости,
- ИСП/спектроскопия,
- тест электрической прочности,
- микробный анализ,
- содержание железа (индекс количественного определения частиц),
- феррография,
- инфракрасная спектроскопия,
- ультрафиолетовая спектроскопия,
- потенциометрическое титрование (общее кислотное число/общее щелочное число),
- анализ осадка.
Мы ничего не пропустили?
2. Анализ вибрации
Анализ вибрации является одним из самых известных методов профилактического обслуживания. Он может обнаруживать перекосы, дисбаланс и износ примерно за 3 месяца до того, как они приведут к поломке. Это также возможность снизить энергопотребление, поскольку, например, водяные насосы с несоосностью потребляют до 15 % больше энергии . Измерение вибрации также широко используется в ISO 22096 .
Методы мониторинга состояния анализа вибрации включают:
- анализ ударных импульсов (например, для вращающегося оборудования),
- быстрый анализ Фурье,
- широкополосный анализ вибрации (например, для обнаружения износа подшипников ),
- ультразвуковой анализ (например, для обнаружения утечек ),
- спектральную плотность мощности,
- анализ временной формы волны (например, для машины с датчиками XY ),
- спектрограммы.
3. Анализ цепи двигателя
Анализ цепи двигателя, также известный (MCA), позволяет оценить состояние электромоторов. Его можно использовать для исследования кондиции (включая роторы, проблемы с муфтой/ремнем, качество электроэнергии), электрического дисбаланса и изоляции. MCA применим не только для предотвращения сбоев, но и для снижения затрат на энергоресурсы и повышения эффективности оборудования на 10–15 % .
4. Термография
Термография изучает распределение тепла и излучения в машинах. Анализ данных делает все остальное, выявляя закономерности, указывающие на отказ или деградацию. Он имеет широкий спектр применений, включая обнаружение несоосности, дисбаланса, неправильной смазки, износа и напряжения в механических деталях. В электрооборудовании он выявляет перегрев, утечки в трубах и слабые места ёмкостей под давлением.
Инфракрасная термография, в частности, стала популярным методом профилактического обслуживания и неразрушающего контроля. Она чрезвычайно эффективна для повышения безопасности, уменьшения количества «слабых точек» и потенциальных причин отказа на 90%. В целом, термография снижает риск, предотвращает сбои и минимизирует затраты и потери.
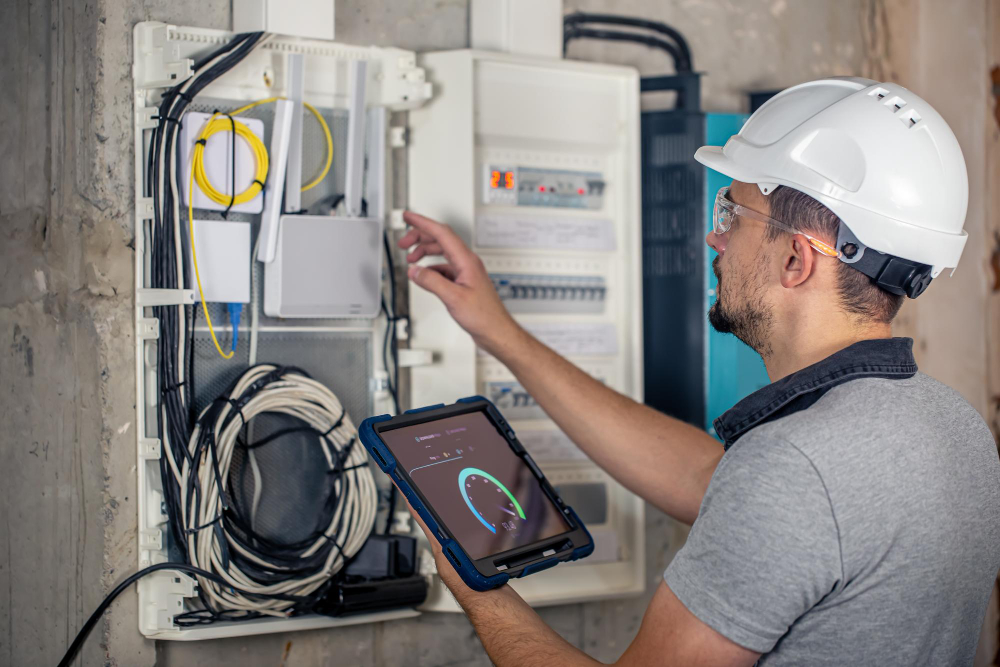
5. Ультразвуковой мониторинг
Мы уже упоминали об этом виде мониторинга в разделе «вибрационный анализ». Но он заслуживает отдельного места в этом списке. Ультразвуковой мониторинг использует высокочастотные волны для обнаружения утечек, посадки деталей и кавитации, что может сократить количество проверок на 30% .
Ультразвуковой мониторинг особенно экономичен, когда он применяется вместе с анализом вибрации (некоторые датчики фиксируют и то, и другое) и инфракрасной термографией. Воздушный и структурный УЗ набирают популярность как хорошие варианты для обнаружения «волн напряжения» на вращающихся механизмах. К другим методам относятся обратное рассеивание и ослабление эха .
6. Рентгенография
Как и термография, радиография (включая радиационный анализ и нейтронную радиографию) является очень тщательным методом неразрушающего контроля. Визуализация позволяет техническим специалистам проверять внутренние дефекты, такие как коррозия в спеченных деталях и изъяны сварки. Однако основным преимуществом является то, что его можно использовать со всеми типами материалов при условии, что мастера используют защиту.
7. Лазерная интерферометрия
Лазерные интерферометры замеряют изменения для расчета смещения на основе длин волн, генерируемых лазером. Они используются при мониторинге состояния для выявления поверхностных и подповерхностных дефектов, таких как коррозия и полости. Интерферометрия включает:
8. Контроль электричества
Чуть более 53% всех случайных бытовых пожаров в Великобритании связаны с возгоранием проводки. Точно так же электричество является одной из основных причин травм и смертельных случаев на работе . Предотвращение сбоев в энергоснабжении с тщательным контролем не только позволяет избежать поломок, но и повышает безопасность. Сюда входят тесты для оценки сопротивления, индукции, емкости, импульсной характеристики, частотной характеристики и деградации.
Методы контроля электрического состояния включают в себя:
9. Электромагнитные измерения
Электромагнитные измерения не следует путать с электрическими. Здесь идет мониторинг искажения магнитного поля для выявления трещин, вмятин, коррозии, слабых мест и других дефектов (например, утонения). Пожалуй, наиболее известным методом такого контроля является вихретоковый контроль (ВКТ), который используется в нефтехимической промышленности для обнаружения плотных трещин.
Помимо ЭТП, существуют и другие методы, такие как:
Эти методы кажутся особенно подходящими для цветных проводящих материалов, таких как трубы, конденсаторы, котлы и поверхности самолетов.
Заключение
Существуют десятки методов контроля состояния и подсчета. Некоторые из них более дорогие, но нет ни одного, который не обеспечивает хорошего соотношения цены и качества.
Мы уже упоминали об этом виде мониторинга в разделе «вибрационный анализ». Но он заслуживает отдельного места в этом списке. Ультразвуковой мониторинг использует высокочастотные волны для обнаружения утечек, посадки деталей и кавитации, что может сократить количество проверок на 30% .
Ультразвуковой мониторинг особенно экономичен, когда он применяется вместе с анализом вибрации (некоторые датчики фиксируют и то, и другое) и инфракрасной термографией. Воздушный и структурный УЗ набирают популярность как хорошие варианты для обнаружения «волн напряжения» на вращающихся механизмах. К другим методам относятся обратное рассеивание и ослабление эха .
6. Рентгенография
Как и термография, радиография (включая радиационный анализ и нейтронную радиографию) является очень тщательным методом неразрушающего контроля. Визуализация позволяет техническим специалистам проверять внутренние дефекты, такие как коррозия в спеченных деталях и изъяны сварки. Однако основным преимуществом является то, что его можно использовать со всеми типами материалов при условии, что мастера используют защиту.
7. Лазерная интерферометрия
Лазерные интерферометры замеряют изменения для расчета смещения на основе длин волн, генерируемых лазером. Они используются при мониторинге состояния для выявления поверхностных и подповерхностных дефектов, таких как коррозия и полости. Интерферометрия включает:
- лазерную ширографию,
- лазерный ультразвук,
- картирование деформации,
- интерферометрию с электронной спекл-структурой,
- цифровую голографию.
8. Контроль электричества
Чуть более 53% всех случайных бытовых пожаров в Великобритании связаны с возгоранием проводки. Точно так же электричество является одной из основных причин травм и смертельных случаев на работе . Предотвращение сбоев в энергоснабжении с тщательным контролем не только позволяет избежать поломок, но и повышает безопасность. Сюда входят тесты для оценки сопротивления, индукции, емкости, импульсной характеристики, частотной характеристики и деградации.
Методы контроля электрического состояния включают в себя:
- проверку мегаомметром,
- испытание на высокое напряжение или испытание на диэлектрическую стойкость (например, чтобы определить, в хорошем ли состоянии изоляция),
- анализ характеристик мощности (для проверки тока и напряжения),
- испытание импеданса батареи,
- испытание на перенапряжение и перенапряжение (также для обнаружения дефекты изоляции),
- в некоторой степени, анализ цепи двигателя.
9. Электромагнитные измерения
Электромагнитные измерения не следует путать с электрическими. Здесь идет мониторинг искажения магнитного поля для выявления трещин, вмятин, коррозии, слабых мест и других дефектов (например, утонения). Пожалуй, наиболее известным методом такого контроля является вихретоковый контроль (ВКТ), который используется в нефтехимической промышленности для обнаружения плотных трещин.
Помимо ЭТП, существуют и другие методы, такие как:
- импульсные вихревые токи,
- вихревые токи в удаленном и ближнем поле,
- испытание вихревыми токами с насыщением низкой частоты,
- массив вихревых токов,
- магнитопорошковая дефектоскопия,
- утечка магнитного потока,
- магнитная память металла.
Эти методы кажутся особенно подходящими для цветных проводящих материалов, таких как трубы, конденсаторы, котлы и поверхности самолетов.
Заключение
Существуют десятки методов контроля состояния и подсчета. Некоторые из них более дорогие, но нет ни одного, который не обеспечивает хорошего соотношения цены и качества.